About Kelsun
Seaweed is one of the most regenerative organisms on our planet and absorbs carbon dioxide in the ocean, similar to trees on land. We combine this with our proprietary formulation to create Kelsun®, a bio-based fiber that can be used across nonwovens and traditional textiles industries.
Interested in purchasing Kelsun®?
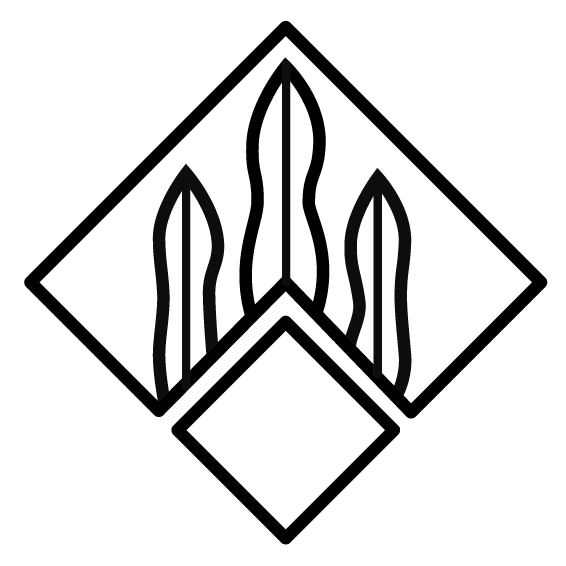
Biobased and Renewable
Made from fast-growing seaweed requiring no fresh water or arable land. Decomposes naturally.
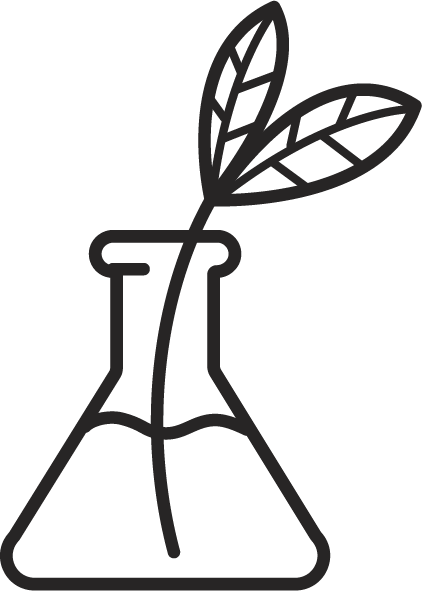
Non-toxic
Safe for humans and the environment with no harmful byproducts.
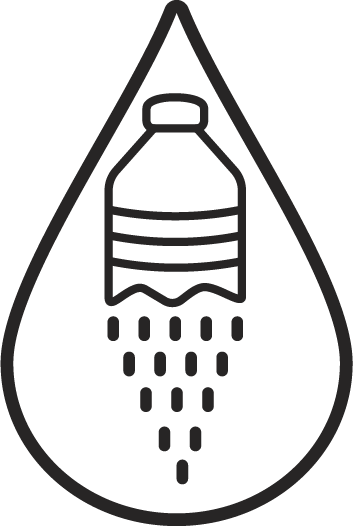
No Microplastics
Contains no plastic and doesn't create microplastics, protecting oceans and ecosystems.
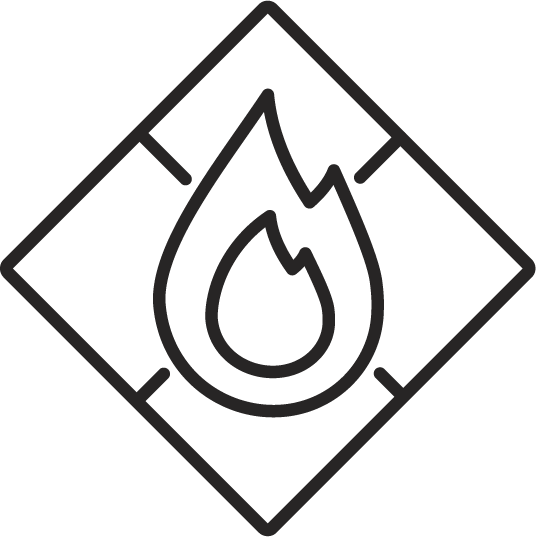
Flame Resistant
Does not ignite and has an inherent ability to self extinguish; no melt, no drip.
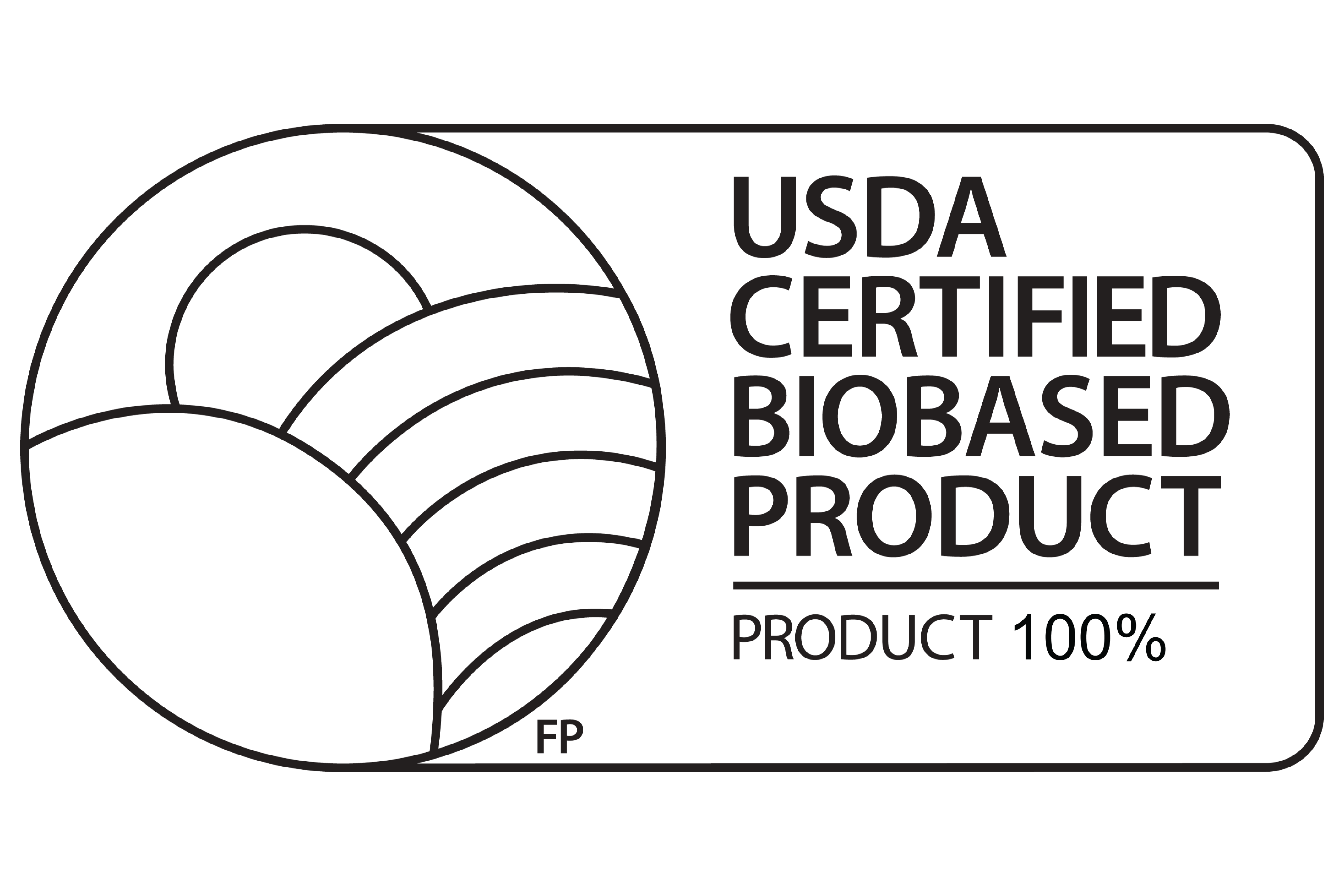
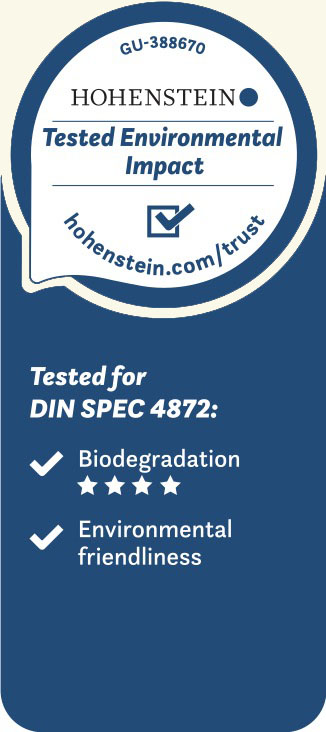
Kelsun® fiber is 100% biodegradable within a few days.
Hohenstein DIN SPEC 4872
Kelsun® fiber contains 100% biobased carbon content.
USDA Biobased Certified
100% Kelsun® fabric reduced bacterial count by 98.6% after 24 hours .
ASTM E2149
Kelsun® fiber is inherently flame resistant.
FMVSS 302